There aren’t many watch companies able to produce their own cases and even fewer can make them in gold. Chopard is one of this exclusive circle.
Over the past two decades, a new psychological bar has been set within the watch industry: in-house movements are regarded as the nec plus ultra – mechanical independence being the best way to legitimize a high-end brand in the eyes of demanding customers. These days, with more and more companies able to produce their own movements and claiming that coveted Manufacture status, the bar might be set differently: by the Midas touch.
Few watch brands are capable of making their own cases, let alone gold cases. Chopard is one of the rare manufacturers mastering the gold case production process from A to Z, due to an in-house foundry where 24-carat fine yellow gold ingots are transformed into five different shades of 18-carat gold alloys, used to shape not only watch cases but also jewellery.
Personality goes a long way
Die-hard aficionados will enthusiastically discuss the aesthetical and technical aspects of Manufacture movements and complications, but watch cases aren’t nearly as fiercely debated – despite the fact that they contribute as much or even more to the personality of a timepiece. If a dial may be considered the face of a watch, the case certainly is the body. Much like in a movement or on a dial, a watch case also requires maximum precision and any watch company that is able to completely control the quality of production will not only save precious time by responding faster to its needs, but also gain an edge on the competition.
Founded by young Swiss watchmaker Louis-Ulysse Chopard in 1860 and bought by a dynasty of German jewellers in 1963, Chopard has now acquired five full decades of expertise in smelting its own gold and creating precious alloys for the brand’s timepieces. The company has three manufacturing sites; Pforzheim, in the German region from where the Scheufele family originally hails, has a facility mainly dedicated to jewellery; Fleurier is where the movements are manufactured; whereas Meyrin (on the outskirts of Geneva) comprises the headquarters and several watchmaking trades – including the workshop where gold cases and bracelets are produced.
Five shades of gold
Each year, Chopard buys at least 2.5 tons of gold – that’s 2,500 one-kilo certified gold bars (corresponding to a 999,9 fineness standard). Every gold bar is smelted and blended with other metals to create various hues of gold: white gold, two shades of yellow gold (2N, 3N) and two tones of rose gold (4N, 5N). Regarding yellow and rose gold hues, silver and copper are mixed in different proportions: for the yellow 2N, it’s 75% gold, plus 16% silver and 9% copper; for the 4N rose shade, the silver amount goes down to 9% while the copper part ascends to 16%. In the case of white gold, palladium is added and then rhodium-plated.
The 18-carat alloy (or 750/1000 gold, meaning 750 grams of pure gold for 1 kilo of matter) instituted by law in most countries is greatly appreciated because it provides an excellent balance between resistance, excellence and fine gold content; it is also ideal for setting precious stones and stands up well to the impacts sustained in daily life, whereas 24-carat gold is too malleable. Pure gold has a hardness of 30 Vickers (2.5 Mohs); while a gold alloy may be ten times as hard (up to 300 Vickers).
Alchemy duo
The gold casting workshop involves two members of staff, headed by Portugal’s Paulo Caetano, who confided in us that Chopard’s 18-carat gold always has a little over the required 750 grams of fine gold. Besides the foundry, the workshop has been equipped with a second vacuum induction oven entirely computerised that serves to cast 6 to 20 kilos of gold at once. Even though new technologies are employed, the Midas touch is still needed: human expertise remains crucial, because gold is made according to a specific recipe and requires carefully controlled gestures in order to obtain the ideal chemistry.
To mix the various components of an alloy together, they are placed in a high heat (around 1000ºC) crucible to combine them and then poured into a mould to form a larger bar. The original thicker bar passes several times through a machine to progressively become a thinner bar of 60x6 cm; further firings at an average temperature of 600°C are needed in order to restore the ingot to its initial structure. It may then be rolled one last time in order to give it the necessary thickness that is required by the creations for which the gold is intended; then each one of those bars is labelled and one corner is cut out to be sent for verification (the amount of precious metal in an alloy) and certification (whether it qualifies for the hallmark) at the Precious Metal Control of the Swiss customs administration.
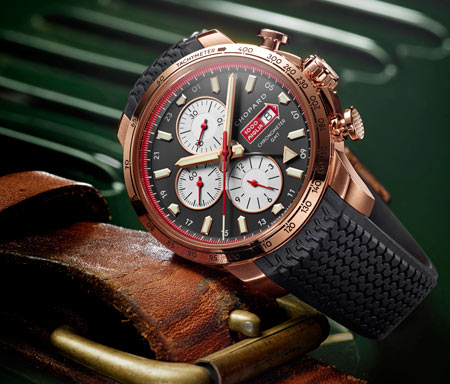
Before the alloy is ready for usage, further firings at around 600°C are needed. The lengthy stamping process generally involves 16 steps to make a watch case, and between each of those steps, the metal is annealed for more than half an hour at high temperature in an oven to relieve the stresses from the stamping and prevent the metal from breaking.
Since the dawn of time, gold has been the stuff of myths, legends and fairy tales – from the Philosopher’s Stone to the famous El Dorado. While no one has yet discovered a way of turning any base metal into gold through mystic alchemical procedures, gold still has the Midas touch. It has been the investment phenomenon of the past decade, frequently hitting new highs, and during that period, investors in gold have made nearly five times their money while Wall Street has gone sideways. So maybe it’s time to think about a gold watch!

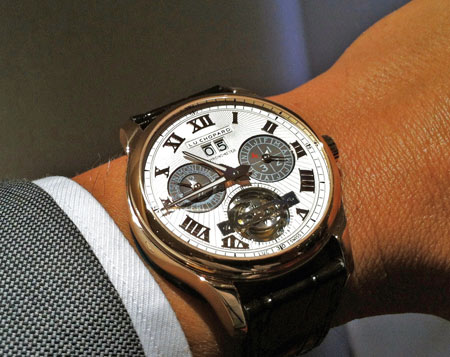
Personality goes a long way
Die-hard aficionados will enthusiastically discuss the aesthetical and technical aspects of Manufacture movements and complications, but watch cases aren’t nearly as fiercely debated – despite the fact that they contribute as much or even more to the personality of a timepiece. If a dial may be considered the face of a watch, the case certainly is the body. Much like in a movement or on a dial, a watch case also requires maximum precision and any watch company that is able to completely control the quality of production will not only save precious time by responding faster to its needs, but also gain an edge on the competition.
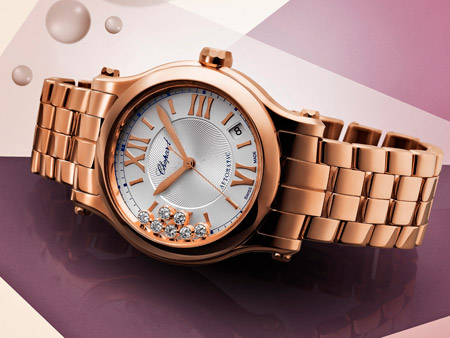
Five shades of gold
Each year, Chopard buys at least 2.5 tons of gold – that’s 2,500 one-kilo certified gold bars (corresponding to a 999,9 fineness standard). Every gold bar is smelted and blended with other metals to create various hues of gold: white gold, two shades of yellow gold (2N, 3N) and two tones of rose gold (4N, 5N). Regarding yellow and rose gold hues, silver and copper are mixed in different proportions: for the yellow 2N, it’s 75% gold, plus 16% silver and 9% copper; for the 4N rose shade, the silver amount goes down to 9% while the copper part ascends to 16%. In the case of white gold, palladium is added and then rhodium-plated.
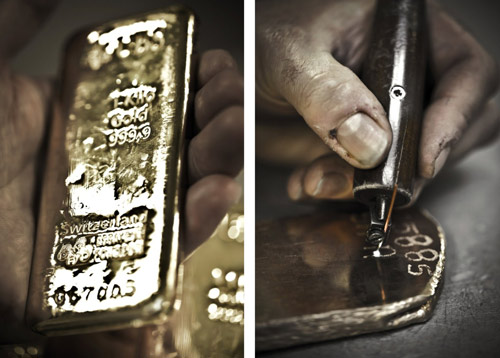
Alchemy duo
The gold casting workshop involves two members of staff, headed by Portugal’s Paulo Caetano, who confided in us that Chopard’s 18-carat gold always has a little over the required 750 grams of fine gold. Besides the foundry, the workshop has been equipped with a second vacuum induction oven entirely computerised that serves to cast 6 to 20 kilos of gold at once. Even though new technologies are employed, the Midas touch is still needed: human expertise remains crucial, because gold is made according to a specific recipe and requires carefully controlled gestures in order to obtain the ideal chemistry.

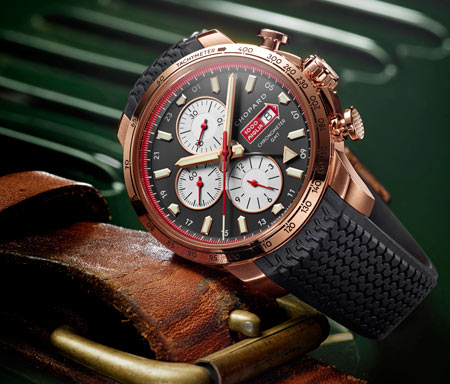
Before the alloy is ready for usage, further firings at around 600°C are needed. The lengthy stamping process generally involves 16 steps to make a watch case, and between each of those steps, the metal is annealed for more than half an hour at high temperature in an oven to relieve the stresses from the stamping and prevent the metal from breaking.
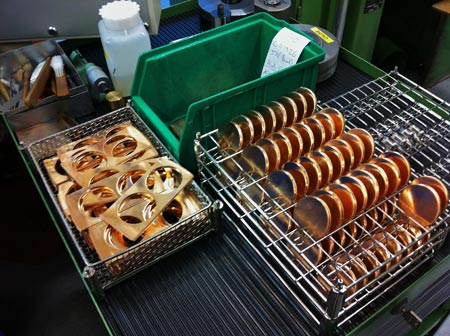

Featured brand